Discover What is Porosity in Welding and Its Effect on Structural Integrity
The Science Behind Porosity: A Comprehensive Guide for Welders and Fabricators
Recognizing the elaborate systems behind porosity in welding is vital for welders and makers making every effort for impressive craftsmanship. As metalworkers explore the depths of this sensation, they uncover a world governed by different elements that affect the development of these minuscule spaces within welds. From the structure of the base products to the details of the welding process itself, a plethora of variables conspire to either exacerbate or minimize the existence of porosity. In this thorough guide, we will certainly unravel the science behind porosity, exploring its impacts on weld quality and introduction advanced strategies for its control. Join us on this trip through the microcosm of welding blemishes, where accuracy satisfies understanding in the search of perfect welds.
Understanding Porosity in Welding
FIRST SENTENCE:
Assessment of porosity in welding discloses vital insights into the honesty and quality of the weld joint. Porosity, characterized by the existence of dental caries or spaces within the weld metal, is a common concern in welding processes. These spaces, otherwise appropriately resolved, can endanger the structural stability and mechanical residential or commercial properties of the weld, leading to possible failures in the ended up item.
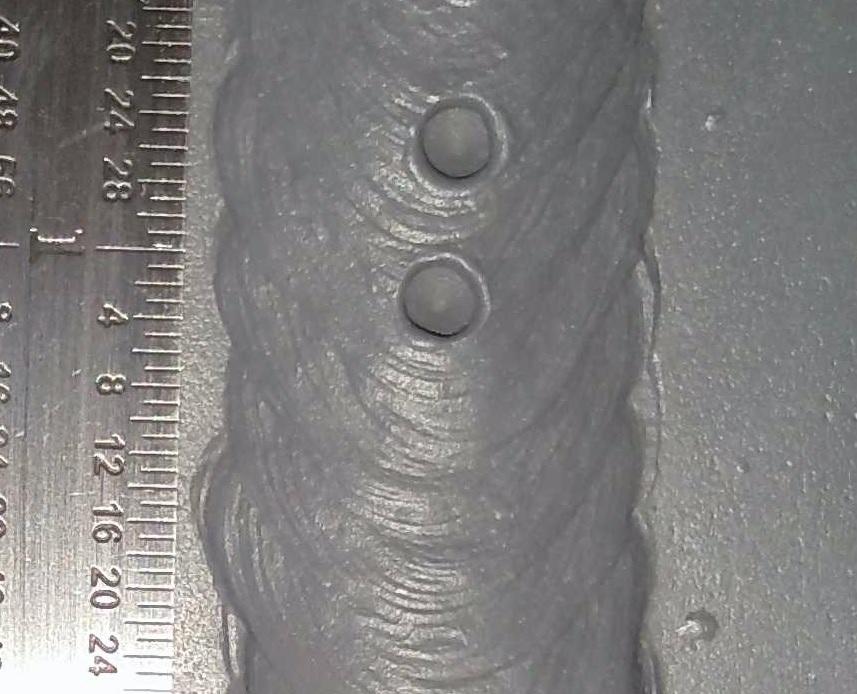
To identify and quantify porosity, non-destructive screening approaches such as ultrasonic screening or X-ray inspection are often used. These strategies permit the identification of interior problems without jeopardizing the stability of the weld. By analyzing the dimension, form, and circulation of porosity within a weld, welders can make enlightened decisions to enhance their welding procedures and achieve sounder weld joints.

Elements Affecting Porosity Formation
The event of porosity in welding is affected by a myriad of elements, ranging from gas securing effectiveness to the details of welding criterion settings. Welding parameters, including voltage, existing, travel speed, and electrode kind, additionally influence porosity formation. The welding method employed, such as gas metal arc welding (GMAW) or protected metal arc welding (SMAW), can influence porosity development due to variants in warm circulation and gas insurance coverage - What is Porosity.
Effects of Porosity on Weld Top Quality
The presence of porosity also damages the weld's resistance to deterioration, as the entraped air or gases within the spaces can respond with the surrounding environment, leading to deterioration over time. Additionally, porosity can prevent the weld's capability to withstand stress or impact, further jeopardizing the general quality and integrity of the bonded see here now framework. In important applications such as aerospace, automobile, or architectural buildings, where safety and security and sturdiness are paramount, the harmful results of porosity on weld quality can have severe repercussions, emphasizing the value of reducing porosity with correct welding techniques and procedures.
Strategies to Decrease Porosity
In addition, making use of the proper welding parameters, such as the proper voltage, current, and take a trip rate, is essential in avoiding porosity. Preserving a constant arc size and angle during welding additionally helps lower the chance of porosity.

Additionally, selecting the right protecting gas and maintaining correct gas circulation prices are essential in lessening porosity. Using the appropriate welding technique, such as back-stepping or employing a weaving activity, can likewise assist disperse heat uniformly and minimize the possibilities of porosity formation. Ensuring appropriate air flow in the welding setting to remove any type of prospective sources of contamination is important for accomplishing porosity-free welds. By implementing these techniques, welders can effectively reduce porosity and produce top quality welded joints.

Advanced Solutions for Porosity Control
Carrying out advanced innovations and ingenious methods plays a pivotal role in attaining exceptional control over porosity in welding procedures. In addition, using innovative welding techniques such as pulsed MIG welding or changed environment welding can additionally company website help reduce porosity concerns.
One more innovative service includes using advanced welding equipment. Utilizing tools with built-in features like waveform control and advanced power sources can improve weld quality and reduce porosity risks. The application of automated welding systems with specific control over specifications can substantially minimize porosity issues.
Furthermore, including advanced surveillance and evaluation modern technologies such as real-time X-ray imaging or automated ultrasonic testing can assist in discovering porosity early in the browse around this site welding process, permitting instant corrective activities. Generally, integrating these innovative services can substantially improve porosity control and improve the general top quality of bonded components.
Final Thought
In conclusion, recognizing the scientific research behind porosity in welding is important for welders and producers to create high-quality welds - What is Porosity. Advanced solutions for porosity control can better boost the welding procedure and make sure a solid and reputable weld.